We have all seen it in one form or another. In packages ordered online, wrapped around fragile products or in our hands as we satisfyingly pop bubble wrap. From everyday household items purchased online to high-value products like electrical and computer components. If there’s a possibility of damage to your product, there’s a protective packaging solution to keep it safe.
Over the years, as businesses attempt to streamline and optimize packaging solutions, protective packaging has evolved. Traditional methods are still very effective and commonly used today, but advances in materials and packaging equipment have helped propel protective packaging into the next generation. Solutions now offer automated packaging options to help reduce labour and waste, while increasing processing speeds for high volume packers.
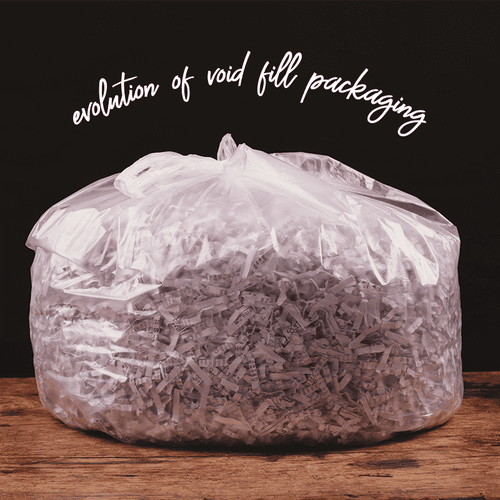